The Theory Of Aluminum Die Casting
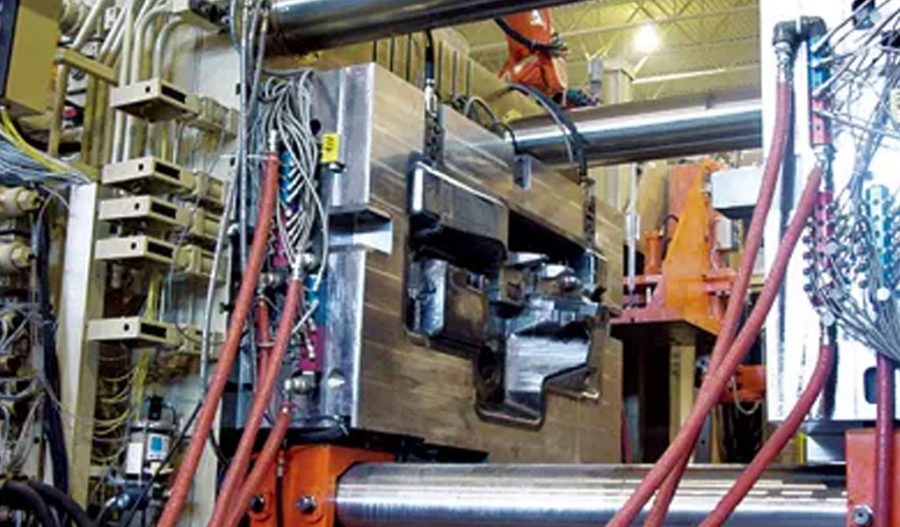
Aluminum alloy die-casting products are mainly used in electronics, automobiles, motors, home appliances and some communication industries. Some high-quality aluminum alloy thin wall die casting products with high performance, high precision and high toughness are also used in large aircraft, ships and other industries with relatively high requirements. . The main use is still on the parts of some instruments.
Casting aluminum alloy ingot production process: electrolytic aluminum liquid, waste aluminum ingot, scrap – batching – smelting tool preheating – slag removal in ladle – furnace loading – mixed smelting – furnace temperature control – slag removal and degassing – casting tool preheating ——Open the furnace hole to release molten aluminum – pouring – slag – cooling into indium – inspection – coding – packing – finished casting of aluminum alloy ingots.
Smelting operation: As described above, the pouring process is basically the same as that of ordinary casting, and the specific operations are related to the smelting of aluminum alloys and the casting of aluminum ingots for remelting.
It is mentioned in the die casting theory of aluminum die castings that continuous casting of horizontal ingot molds is the most commonly used casting method in aluminum electrolysis plants. Aluminium ingots for remelting of aluminium and aluminium alloys. A special volume die casting machine is used to realize this casting.
The horizontal continuous ingot casting method is a casting method with a high degree of mechanization of the block iron mold ingot casting method. The die casting mold technology is relatively simple. Because the aluminum alloy ingots for remelting are produced, the defects on the surface of the ingots and the requirements for the internal crystalline structure are relatively not strict. There are still requirements for pinhole grades inside the ingot. For the specific requirements of die casting ingots, please refer to the standard "Casting Aluminum Alloy Ingots"
Die Casting Process Control
The requirements for the process of horizontal continuous casting are mainly pouring temperature, pouring speed and water cooling control(The Theory Of Aluminum Die Casting).
- Pouring temperature The casting temperature of aluminum and aluminum alloy ingots for re-cultivation is different due to the different alloy varieties. In general, the pouring temperature of common aluminum and deformed aluminum alloys is in the range of 30-80 degrees above the crystallization temperature of the alloy. Cast aluminum alloys are in the range of 30 – 50 degrees above the crystallization temperature.
- Pouring speed Horizontal ingot mold continuous casting is a fixed casting machine. Different types of casting machines have different casting speeds. The casting speed is adjustable, and the casting speed is expressed by the travel speed of the mold. But to be more intuitive, foundries generally test casting speed by casting several ingots per minute. It should be emphasized that the casting speed should not be adjusted too fast, otherwise, it may cause the die casting machine to vibrate greatly, and the ingot will have serious ripples and surface oxidation.
- Cooling control The cooling method of the horizontal ingot mold continuous casting machine is divided into two types: one is the forced water-cooling type immersed at the bottom of the casting mold, which mainly controls the inlet water temperature to be below 40 degrees and the return water temperature to be below 60 degrees. The other is the natural cooling method of the ingot, but in order to ensure the normal operation of the casting machine, it is necessary to reduce the temperature of the casting mold, and spray cooling with water before or after the demoulding of the ingot, so as to reduce the temperature of the casting mold, that is, to avoid die casting mold cost.The equipment failure that may occur in the high temperature operation of the casting machine is also conducive to the demolding of the ingot and the stability of the process conditions. This cooling method generally requires the water spray temperature to be below 40 degrees.